Assembly Line Improvements
Assembly Line Improvement Increases Capacity by 22% while Improving Product Quality and Decreasing Costs
Situational Overview
A $200M equipment manufacturer produced control valves using two methods: modern assembly line and the traditional workbench. Assembly via workbench was easy to setup, but less efficient and plagued with quality problems. Defects and rework using the workbench method were running almost double in comparison to the assembly lines.
Solution
A team participated in Lean Six Sigma training to identify the root causes for higher defects on workbenches. They determined that assembly lines had a higher degree of standardization and piloted moving two products from workbenches to a modified assembly line. Some best practices from workbenches, such as upgrading from pneumatic to digital torque wrenches, were applied to the lines.
Results
The Lean Six Sigma projects were very successful. Both quality and efficiency increased, and the two valves used in the pilot were permanently moved to assembly line production. The line capacity increased by 10,000 units per year, a 22% increase, and assembly cost was reduced by 12.5%.
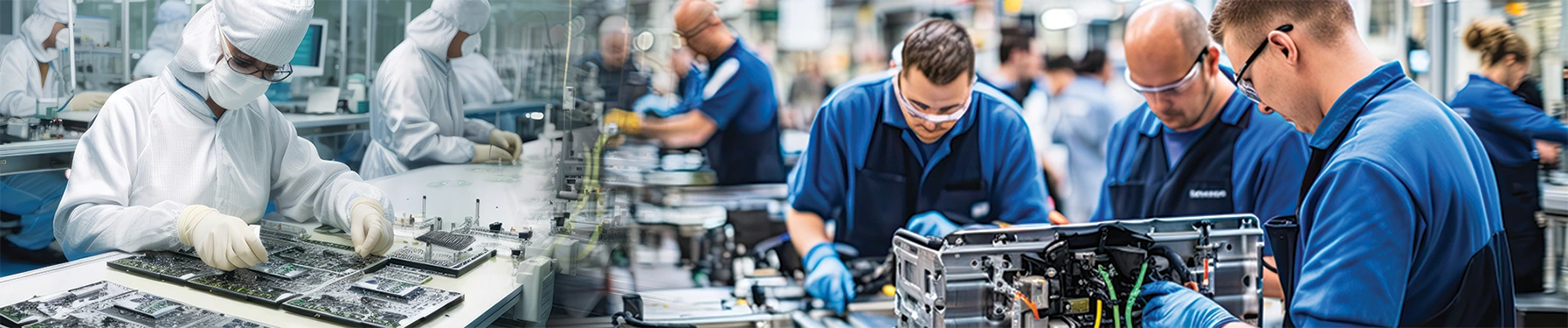
For more information on this topic, as well as how Corporate Education Group can help power your organization’s performance, contact us via email or call 1.800.288.7246 (US only) or +1.978.649.8200. You can also use our Information Request Form!

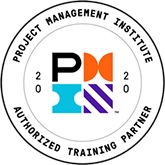
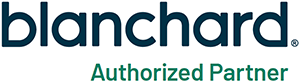

- ©2025 Corporate Education Group, operated by CEG Operating Company, LLC. All Rights Reserved.
Privacy Policy | Terms and Conditions - PMI®, PMP®, CAPM®, PgMP®, PMBOK®; and the PMI®; Registered Education Provider logo are registered trademarks of the Project Management Institute, Inc. CBAP® and IIBA® are registered trademarks of International Institute of Business Analysis. All other trademarks mentioned on this site are property of their respective owners. All rights reserved. CEG is an approved Authorized Partner within the Blanchard Authorized Partner Program and is licensed to market, sell, and train SLII®.